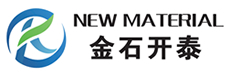
Although the specifications and properties of electrolytic copper foil have their own characteristics due to the different copper foil manufacturing enterprises, the manufacturing process is basically the same. That is, electrolytic copper or scrap copper wire with the same purity as electrolytic copper is used as raw material, dissolved in sulfuric acid to make an aqueous solution of copper sulfate, with a metal roller as the cathode, through the electrolytic reaction to continuously electrolytically deposit metal copper on the surface of the cathode roller, and continuously peel from the cathode roller, this process is called foil electrolysis process. Finally, the side (smooth surface) peeled from the cathode is the side of the laminate or printed circuit board surface, and the reverse side (commonly known as the wool surface) is the side that needs a series of surface treatment and is bonded with the resin in the printed circuit board.
Principle of electrolysis
During electrolysis, the cations in the electrolyte migrate to the cathode, and the electrons are reduced on the anode. The anions run to the anode and lose electrons to be oxidized. Two electrodes are connected in the copper sulfate solution and direct current is applied. At this time, copper and hydrogen will be found on the plate connected to the cathode of the power supply. In the case of a copper anode, the dissolution of copper and the precipitation of oxygen occur simultaneously. The reaction is as follows:
cathode:Cu²+2e→2Cu
2H++2e→H2↑
Anode:4OH-+4e→2H2O+O2↑
2SO24+2H2O-4e→2H2SO4+O2↑
The copper dissolved from the anode complements the consumption of copper ions in the electrolyte. After a certain treatment of the cathode surface, the copper layer deposited on the cathode can be peeled off, and a certain thickness of copper skin will be obtained. Copper skin with a certain function is called copper foil.